Tungsten Carbide Knives Thermal Fatigue Mechanism
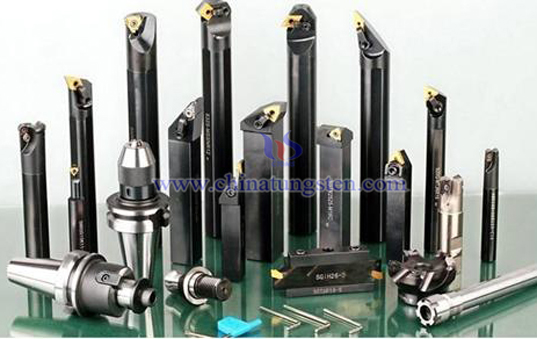
Tungsten carbide knives make a kind of refractory metal compounds (WC) as the matrix, and make of transition metals (Co, Fe, Ni) as the binder phase, produced by powder metallurgy method. Tungsten carbide knives with high strength, high hardness, high elastic modulus, wear resistance, corrosion resistance, low thermal expansion coefficient and more stable chemical properties, etc., in the industry has been widely used.
Tungsten carbide knives at high speed, especially in the intermittent turning and milling process, Tungsten carbide knives to constantly subjected to thermal shock when heated due to the cutting and retracting cutting fluid cooling and cooling caused by very easily formed inside the tool temperature gradient, thermal stress and mechanical stress causes the tool joint action easily fatigue breakage, so that premature tool failure. Therefore, the study carbide thermal fatigue mechanism is important.
Tungsten carbide knives in the course will continue under alternating bending stress, thermal shock stress changes periodically frequent mechanical shock and cut and cut out when the temperature of the workpiece caused thereby resulting in surface cracks and chipping occur stick knives . The reason the surface cracks due to thermal expansion and contraction of materials is to generate a temperature difference between the inside and outside materials, thermal shock resistance of metallic materials the size of the material depends on the strain of thermal conductivity and thermal expansion produced. Tungsten carbide knives during frequent staging and cut out parts, the local temperature up to 1000 ℃, the thermal expansion coefficient of different materials in different regions of the tool, as it generates heat stress in the coolant or air cooling effect, when the stress is too hot large, it will lead to the formation of surface cracks. Meanwhile, the tungsten carbide knives and the workpiece heat caused by friction between the internal temperature of the uneven distribution of the hook tool, the tool will be varying degrees of fracture failure. The main reason for the thermal fatigue crack initiation, expansion, resulting in the tool failure. Carbide thermal fatigue cycle by periodic changes or effects of temperature, the material crack initiation and propagation.
Although harder than carbide ceramics, cubic boron nitride and diamond slightly lower, but better than ordinary carbon steel, and high speed steel is much higher than high-speed steel,and toughness slightly lower than high-speed steel, but better than ceramics, cubic boron nitride and diamond, that determines the tungsten carbide knives industry in an irreplaceable position.