Tungsten Carbide Knives
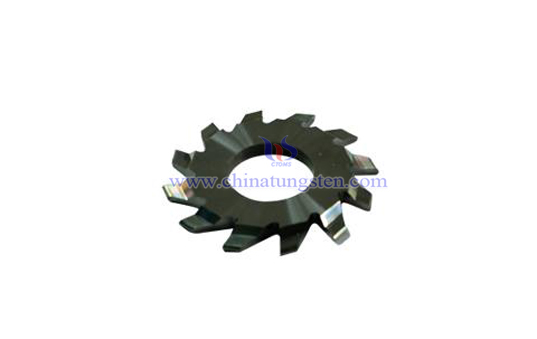
Traditional carbide materials (including coated tungsten carbide knives) its composition and properties from the table to basically the same, there is a contradiction between hardness and toughness: To obtain a high toughness, hardness must be sacrificed; and to obtain high hardness, toughness must be sacrificed. This makes the application of traditional carbide materials are subject to certain restrictions. The gradient coating matrix tungsten carbide knives, after coating, to make tungsten carbide knives also have good wear resistance, hardness and strength.
Gradient coating matrix tungsten carbide knives sintering is typically a two-step, the first step: calcined, calcined process is carried out under nitrogen atmosphere, to below 400 ℃ 4-5 ℃ / min rate of heating, the temperature reached about 1390 ℃, at this temperature for about l hour, followed by furnace cooling the sample. Calcined dewaxing and deoxidation mainly in order to obtain a dense sintered body in the subsequent sintering process, and to prevent the formation of a graded structure in the pre-burn stage. Step Two: gradient sintering, the calcined product by heating in a vacuum state, the temperature was raised to 1420 ℃ after incubation for 2 hours, thereby missing cubic carbides and carbonitrides are formed in the surface of the alloy toughness region. In the sintering process, a nitrogen-containing carbide, nitrogen plays an important role, with nitrogen (to carbonitride, nitride, or in the form of nitrogen) was added, the sintering process of the metallurgical reaction becomes more complicated, but also atmosphere more stringent control requirements.
Bonding strength between the coating and the interface has a great influence on the reliability of the Gradient coating matrix tungsten carbide knives material, therefore, in addition to carbon content control interface, it also should be possible to control the presence of other defects at the interface, for example, the interface appears to avoid coarse grain WC, WC grain size and distribution at the interface drilling phase should be as uniform.