硬质合金刀具超高速切削机理
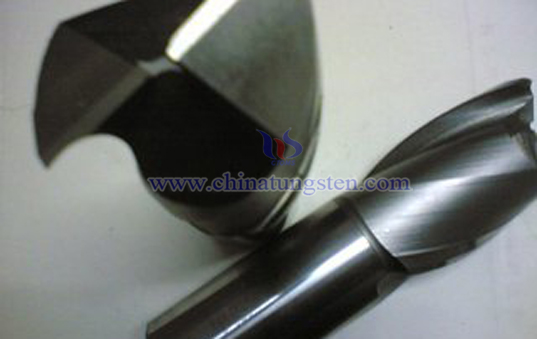
随着加工工业的发展,现代刀具材料向着高精度、高速切削、干式切削和降低成本等方向发展。硬质合金刀具以其优良的性能正在更多的场合替代其他的刀具材料。它是由难熔金属化合物和金属黏结剂经粉末冶金方法制成的工具材料。硬质合金刀具硬度为HRA89~94,远高于高速钢,且具有化学稳定性好、耐热性高等优点。
从微观上来看,晶体并不是刚体而是弹性体。而且由于构成晶体的原子和晶体结构的不同,其刚性、弹性、晶体强度和传递冲击能量的能力完全不同。在硬质合金刀具受到冲击时,冲击能量由冲击点向材料深处扩散。随着冲击速度的提高同样的材料上接受到的冲击能量就越难以传递到材料深处。当到达一定的冲击速度冲击能量会聚集在接触点一定距离内的晶格之间,使得原子震动增加。宏观上硬质合金刀具就表现得如同软质金属一样的加工性质。此时的冲击速度就是此材料相变超塑性现象产生的临界速度。此时的切削速度也就是此材料的超高速切削的临界且须速度。随切削速度的增大, 切屑底层的超塑性层厚逐渐减薄。这就是硬质合金刀具超高速切削时切屑变形的机理和本质。
在硬质合金刀具的超高速切削中,切屑底层金属组织出现了相变超塑性现象。由于超塑性的出现, 变形力明显减小, 没有加工硬化现象, 试样变形后的弯曲率加大。超高速切削时的许多物理现象, 实际上是金属材料由塑性向超塑性的一种转变。主要作用机制是金属材料的超塑性。只要切屑的变形速率和温度达到某一高度值以后,切屑底层就能表现出相变超塑性现象。
因此, 切削力下降,工件变形减小,工件表面温度低,无加工硬化等。当然,不同的金属材料,相变超塑性转变的变形速率和温度也各不相同。