硬質合金刀具超高速切削機理
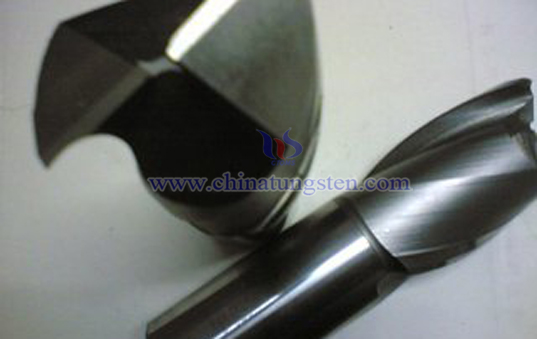
隨著加工工業的發展,現代刀具材料向著高精度、高速切削、幹式切削和降低成本等方向發展。硬質合金刀具以其優良的性能正在更多的場合替代其他的刀具材料。它是由難熔金屬化合物和金屬黏結劑經粉末冶金方法製成的工具材料。硬質合金刀具硬度為HRA89~94,遠高於高速鋼,且具有化學穩定性好、耐熱性高等優點。
從微觀上來看,晶體並不是剛體而是彈性體。而且由於構成晶體的原子和晶體結構的不同,其剛性、彈性、晶體強度和傳遞衝擊能量的能力完全不同。在硬質合金刀具受到衝擊時,衝擊能量由衝擊點向材料深處擴散。隨著衝擊速度的提高同樣的材料上接受到的衝擊能量就越難以傳遞到材料深處。當到達一定的衝擊速度衝擊能量會聚集在接觸點一定距離內的晶格之間,使得原子震動增加。宏觀上硬質合金刀具就表現得如同軟質金屬一樣的加工性質。此時的衝擊速度就是此材料相變超塑性現象產生的臨界速度。此時的切削速度也就是此材料的超高速切削的臨界且須速度。隨切削速度的增大, 切屑底層的超塑性層厚逐漸減薄。這就是硬質合金刀具超高速切削時切屑變形的機理和本質。
在硬質合金刀具的超高速切削中,切屑底層金屬組織出現了相變超塑性現象。由於超塑性的出現, 變形力明顯減小, 沒有加工硬化現象, 試樣變形後的彎曲率加大。超高速切削時的許多物理現象, 實際上是金屬材料由塑性向超塑性的一種轉變。主要作用機制是金屬材料的超塑性。只要切屑的變形速率和溫度達到某一高度值以後,切屑底層就能表現出相變超塑性現象。
因此, 切削力下降,工件變形減小,工件表面溫度低,無加工硬化等。當然,不同的金屬材料,相變超塑性轉變的變形速率和溫度也各不相同。